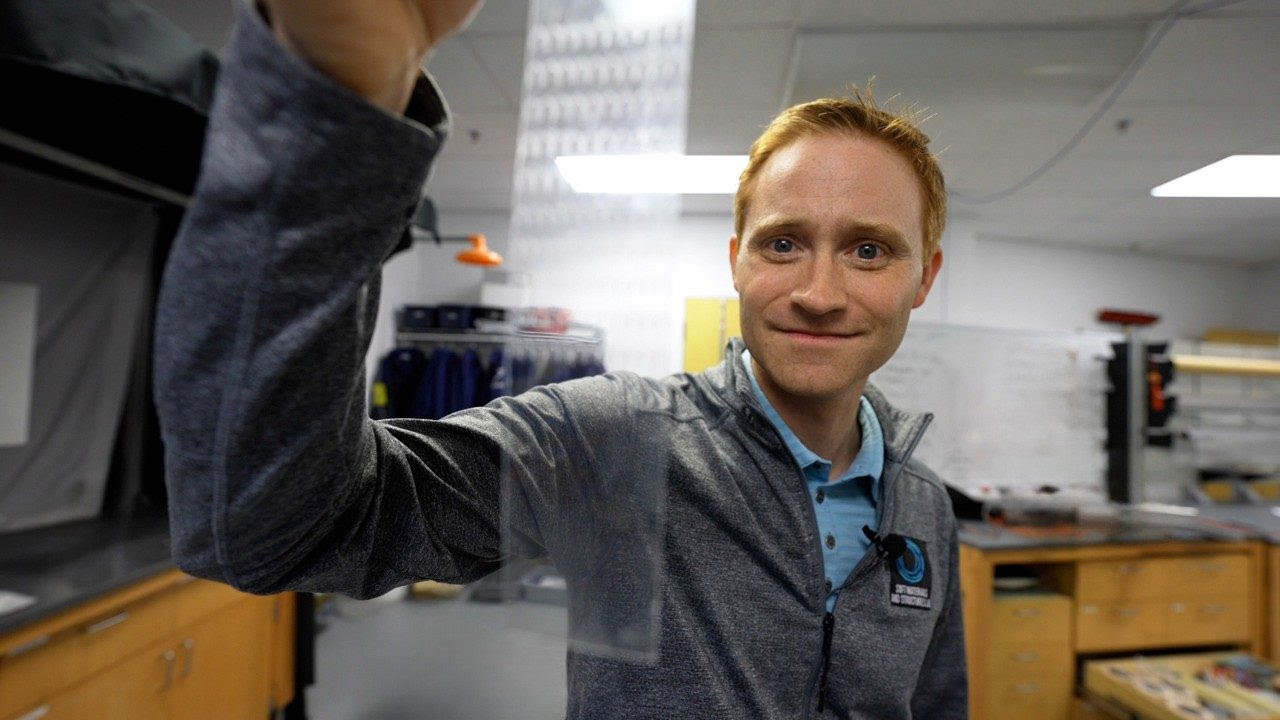
Adhesive tape fulfills many purposes, from quickly fixing household appliances to ensuring a reliable seal on a mailed package. When using tape with a strong bond, removing it may only be possible by scraping and prying at the tape’s corners, hoping desperately that surface pieces don’t tear away with the tape.
But what if you could make adhesives both strong and easily removable? This seemingly paradoxical combination of properties could dramatically change applications in robotic grasping, wearables for health monitoring, and manufacturing for assembly and recycling.
Developing such adhesives may not be that far off through the latest research conducted by the team of Michael Bartlett, assistant professor in the Department of Mechanical Engineering at Virginia Tech, and published in Nature Materials on June 22.
The physics of stickiness
Adhesive tapes were first developed in the 1920s to meet a need for automobile painters who wanted better options for painting two colors on car bodies. Since the first masking tape was put into use, many other variations have been created. Factories have rolled out invisible tape for wrapping presents, electrical tape for covering wires, and duct tape for more uses than it was ever intended to fill.
Normally, when tapes are peeled off, they separate in a straight line along the length of the strip until the tape is completely removed. Strong adhesives are made more difficult to peel, while reusable adhesives promote the strength-limiting separation.
Bartlett’s team theorized that if the separation path were controlled, then perhaps adhesives could be made both strong and removable. They tapped into the methods of a 2,000-year-old Japanese art form to determine how to do it.
Making the cut
The art form of kirigami, through folding and cutting, can transform a flat sheet of paper into a shape or even a three-dimensional object. Children often use a basic form of this method when creating paper snowflakes.
But the research team was making more than snowflakes. Because of kirigami’s artful origins, the method provided a framework for establishing slices or cuts across an adhesive. Bartlett’s team used these principles to engineer a series of U-shaped cuts.
“We realized that by using cuts, we could control how an adhesive separates,” said Bartlett. “An engineered cut can force the adhesive separation path to go backwards at specific locations, which we call reverse crack propagation, making the adhesive very strong. But by peeling in the opposite direction, it always goes forward, making it easy to remove. This is quite unusual behavior, but it is very useful to make strong yet releasable adhesives.”
Bartlett’s team, which also included Associate Professor Rong Long from the University of Colorado Boulder and Assistant Professor Eric Markvicka from the University of Nebraska Lincoln, found that applying these cuts made the bond of the tape stronger by a factor of 60 while still allowing for easy removal by peeling in the opposite direction. The team also found that the type of tape didn’t matter. Kirigami increased the bonds of every type of tape tested, from packaging tapes to medical tapes. In all cases, strong adhesive bonds become even stronger and normally weaker adhesives increased in strength, too.
“What really matters is the shape and size of the cut,” said former graduate researcher Dohgyu Hwang. “We do not have to rely on the specific adhesive material, but as long as the cuts are made at a characteristic size, which is defined by the physics of the adhesive, we found that this enhanced adhesion in every system we tried.”
The other interesting outcome of this approach is that it can be highly customized.
“By placing the cuts in specific locations, we can activate this reverse crack propagation to tune adhesion strength at any film location and it further enables the programming of adhesive strength in two directions simultaneously in a single region of a film. We also use a rapid digital fabrication approach, so we can quickly create highly customizable adhesives with tunable strength. This is a very exciting methodology for the development of future adhesives,” said Bartlett.
Better tape for diverse applications
In a dramatic test for applications, the team applied the same type of tape to two cardboard boxes, sealing them as one might for shipping. One of the tapes had the application of kirigami cuts and the other did not. Researchers then dropped a brick onto the lid of each box. For the unaltered tape, the bond was broken after two drops, collapsing the lid of the box and allowing the brick to enter. However, the altered tape resisted the drops, and on the third attempt, the brick even bounced off the lid.
“This was a very exciting result,” said graduate researcher Chanhong Lee. “We can use normal packaging tapes and make them stronger where needed, but still allow for them to be released. This is very useful for packaging that’s reusable as well, potentially playing a role in sustainability.”
In another test, the team boosted the sticky strength of objects other than tapes. After applying kirigami cuts to a glove used by football players to catch the ball, Lee placed his gloved hand flatly on a sheet of plastic. Both an altered and unaltered glove were abrasive enough for the researcher to hold the plastic at a 90-degree angle, but the unaltered glove lost its bond after a few seconds. The altered glove continued holding the plastic fast, until the researcher eventually laid it down.
“It is common to make adhesive bonds stronger but harder to remove,” said Bartlett. “It’s also common to make those bonds less strong but easy to remove. The challenge is making it both stronger and still easy to remove, and that’s what we’ve achieved.”
Suzanne Miller for Virginia Tech