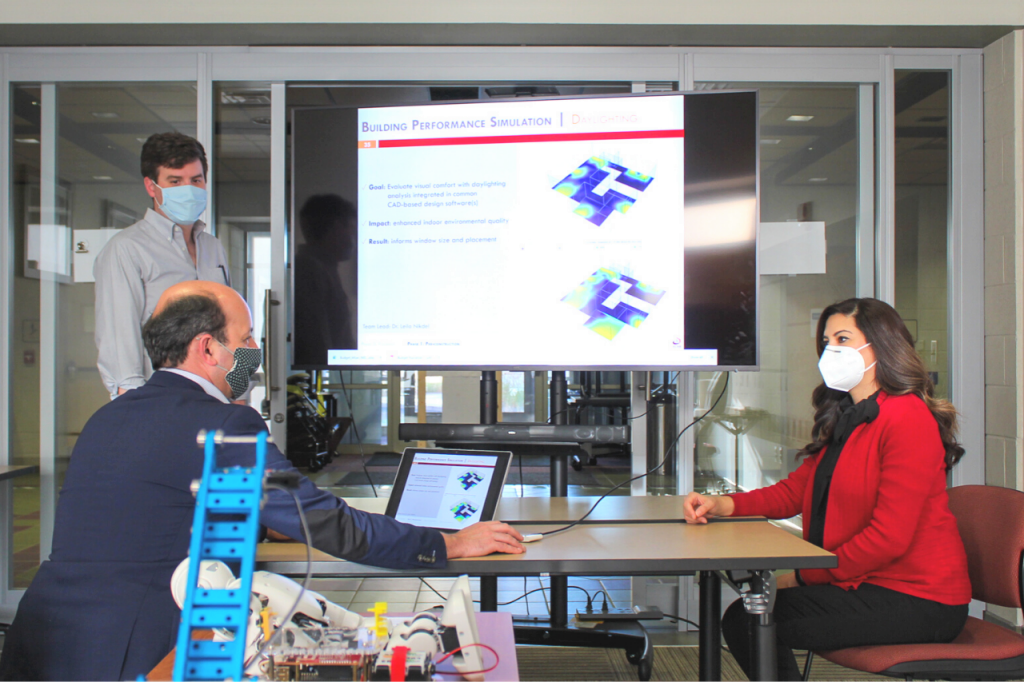
Home ownership has long been a hallmark of the American Dream. But the rising costs of homes, land, and materials — coupled with stagnating incomes, a growing population, increased housing demand, skilled construction labor shortages, a straining rental market and a global pandemic — have pushed the dream of home ownership even further out of reach for many Americans.
Through two vanguard public-private partnerships, Virginia Tech faculty and students in the Myers-Lawson School of Construction (MLSOC) are pursuing low-cost, high-tech and data-driven approaches to making home ownership more attainable. They are exploring the use of concrete 3D-printing technology in building affordable homes in Virginia.
The Virginia Center for Housing Research (VCHR) is an interdisciplinary research center within the College of Architecture and Urban Studies and the official housing research and information center for the Commonwealth of Virginia, is helping pilot two initiatives to determine whether 3D-printed concrete homes and manufactured factory-built housing are viable answers to the housing affordability crisis in Virginia and across the nation.
The first project, “Printing for Affordable Concrete Housing and Training (PACT),” aims to design and produce a 3D-printed single-family concrete home in the greater Richmond metropolitan area. Researchers will print the 1,400-square-foot home on site using a massive, modular 3D-printer called COBOD2, a technology pioneered by the Danish that readily adapts to any location and design.
The study will be the first 3D concrete build in Virginia and the first in the nation to explore the potential of 3D-printed concrete homes for superior cost-efficiency, build time and durability versus traditional stick-built homes in affordable housing.
The Virginia Tech team includes co-principal investigator Philip Agee, an assistant professor cross-appointed in the Department of Building Construction and VCHR. He will study simulated and measured building performance outcomes such as energy use and indoor environmental quality, as well as the human factors resulting from automating common construction tasks.
Virginia Tech students in the Vecellio Construction Engineering and Management program will participate as part of the research team in the designing, printing and evaluation of the home. They will also help determine appropriate future markets and applications for 3D-printing. Virginia students in grades K-12 will be invited to watch as the home is printed and learn about the emerging field of 3D technology in housing construction.
In a second project, Agee is the principal investigator for “Innovations in Manufactured Housing,” which will study new factory-built modular homes as higher-quality, affordable alternatives to older mobile and stick-built homes.
Virginia Tech students will get hands-on experience using building information modeling (BIM) to design and develop 3D models and digital twins of the homes. They will use BIM to evaluate and compare the production process, energy efficiency and operational performance of both site-built and off-site manufactured homes.
“Manufactured housing represents the largest source of unsubsidized affordable housing in the U.S., so increasing the supply of quality manufactured housing will help us more quickly address affordability and home ownership challenges in our state and nation than other housing supply approaches,” Agee said. “This study aims to demonstrate that the manufactured housing of today is a high-quality, affordable housing option.”
Work on both projects is already underway with the 3D-printed home slated for completion in summer 2021 and the first manufactured housing units completed in late 2021.
— Written by Marya Barlow