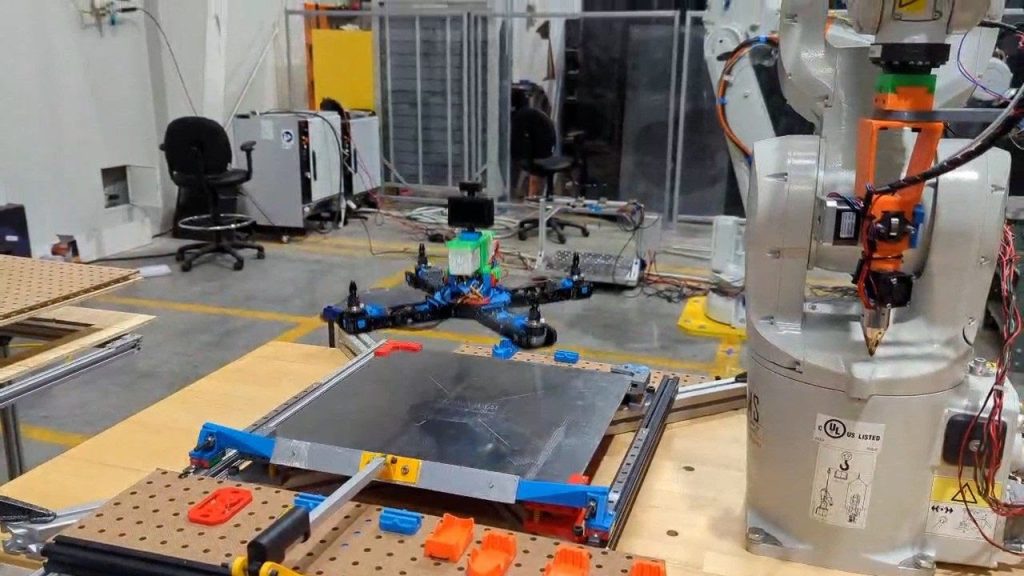
3D printing typically involves a single machine creating an object, but a team of undergraduate researchers has taken that paradigm far outside its box in the Design, Research, and Education for Additive Manufacturing (DREAMS) Lab, led by L.S. Randolph Professor Chris Williams.
The project started with the goal of 3D printing a drone that could autonomously fly out of the printer and evolved into a highly robust, adaptable approach for manufacturing large mechatronic systems.
Drones are complex mechanisms with spinning propellers, precisely calibrated electronics, batteries, and an array of other pieces and parts. One of the team’s early challenges was approaching that complexity with 3D printing. Some parts, such as a charged battery and motor, simply couldn’t be printed and instead required assembly. This assembly doesn’t fit with the normal function of a 3D printer, which is to lay down stacked layers on top of one another, forming a single stationary object.
The team also needed to solve a somewhat sticky problem: setting the drone free. Because a 3D printer’s first layer slightly adheres to the build plate, the team needed to figure out how to scrape the printed piece off during the autonomous process.
A typical 3D printer wouldn’t achieve all these objectives. While the machine can place layers to create a shape and even print different materials together, it cannot grab components and assemble them, and it cannot scrape off its own product. Determining how to complete all those steps autonomously would be the critical factor in creating a working drone that successfully departed its maker.
The box becomes an arm
The team planned to circumvent the typical 3D printer’s function that uses a print head on a fixed gantry. Instead, the group used a robotic arm that could be equipped with tools for printing and component assembly. Although the arms take more work to program and operate, they also offer more options.
“By attaching a print head to multi-axis industrial robotic arms, we gain additional degrees of freedom of movement that allows us to finally print in true 3D,” said Williams. “Instead of just stacking a series of two-dimensional prints of each layer, the kinematic flexibility of the robot arm allows us to deposit material in any direction in 3D space.”
Breaking the bond
After the students designated parts for either printing or assembly, they needed to determine the best way to break the sticky bond between the finished piece and the build plate. This became a lesson in thermodynamics.
The robotic printer’s large, heated build plate, which acts as a base for the piece being built, is slightly warm to create enough adhesion so that the piece doesn’t move during printing. Though essential to achieving the precision required to build, it created an obstacle for a printed piece that needs to fly away from its printer.
Team member Dalton Phillips discovered a surprisingly simple solution to remove the printed piece: let it cool. If the plate cooled a few degrees after the print finished, the adherence became weaker. Once the plate cooled to a certain point, a simple mechanical scraper could be used to push it away. This approach worked, and the drone could be set free.